It all started in an orchard in California in the early 20th century when WO Bentley was still a boy on a bicycle. The remaining root of a dozen-year-old walnut tree shows off unique ridges. Today, the lines still sparkle in the Bentley car. The job of Adrian Minshull, a wood pick expert, is traveling to Italy and elsewhere to import these impressive stumps. He appraised thousands of walnut stumps so there was quite a bit of evaluation experience. Minshull can accurately estimate how much of each vehicle’s interior is sufficiently decorated when a piece of wood is cut into 0.6mm thin leaves. The boards at the base are more valuable than the upper body.
“I have chosen wood for seven years, assessing its origin or quality and usability,” Adrian said . Walnut wood is the most familiar, but does not mean the Crewe factory uses only this type of wood. British oak wood is also available but increasingly rare, so the British car company has introduced two types of mimosa and vavona. Because the species is endangered, mahogany is not used. Wood like the “bird’s eye” is also a special pattern but this wood is very difficult to process. Some customers choose walnut wood for car parts.
“We produce wood for nine four-door cars and several two-door cars a day,” said Adrian . Adrian started working at the factory as an apprentice when he was 16 years old, and went to Wood Shop – the division of Bentley cladding wood processing – at the age of 21. Aridan’s father has been at Crewe for 25 years and his twin brother also works there.
Nowadays such wood paneling is very rare. Most auto manufacturers that supply wood paneling use presses that create very high pressure. This causes the wood to lose its natural properties, so bleaching and staining are needed.
The individual wood panels on each Bentley are unique, and from the start of the production process, it is numbered to coincide with the chassis number of the vehicle intended to be decorated, so that from each thin wooden leaf can be go back to the tree that produced that wood.
Today, on average, each car uses about 60% more wood cladding than 20 years ago. The Wood Shop uses 16 wooden blades to create 26 central components in a Bentley, plus an additional 8 leaves for the handrails. Options such as a picnic table or door panels supplement can increase the total area of wood in a Bentley up to 6.5 m 2 .
Taking advantage of the wood grain duplication at the base, the leaves are doubled up to create a symmetrical visual effect. For example, four leaves are folded in sequence to form a symmetrical pattern across the center of the dashboard, and this pattern reappears and repeats in the dashboard to create a floor effect throughout the vehicle. The railings also show a different pattern, with the same pattern repeated on each door.
It takes 13 days to produce a full set of polished wood cladding. The wooden leaves are shaped, pressed and combined with decorative wood mosaic. The wood paneling requires matching to the instrument panel or curved surface as on the dashboard or console, but the material is very easy to break. Therefore, they must be done in a room with appropriate humidity to keep the necessary elasticity.
80 craftsmen who work in Wood Shop all undergo rigorous skill tests, with at least 8 apprentices. In the machine area, bulk wood is cut to length and stored, using computer-controlled 5 and 3-axis routers (currently unique in the automotive industry) to achieve shapes. The most complex form.
Handrails, mirror edges and picnic tables are sometimes made using traditional woodworking techniques. “We harness technology because of speed, but still retain all the core skills in woodworking,” said Adrian.
Each car is then cleaned and prepared manually, the process takes 5 and a half hours, after which the car is ready to be put into lacquer spraying environment. The lacquer used today is environmentally friendly, shiny and virtually non-ripple. It is painted in 5 layers and takes 3 days to complete before starting the work of removing blemishes to achieve a mirror-like shiny surface.
The paneling is sandpapered using a sand belt but mostly by hand, using up to five sandpaper files. Finally, come to the finishing area and polish with wax before rubbing the ball with polishing wipe. Cladding after finishing polishing process will have high durability and ability to withstand the damage from outside.
The feats of wooden furniture of Bentley cars
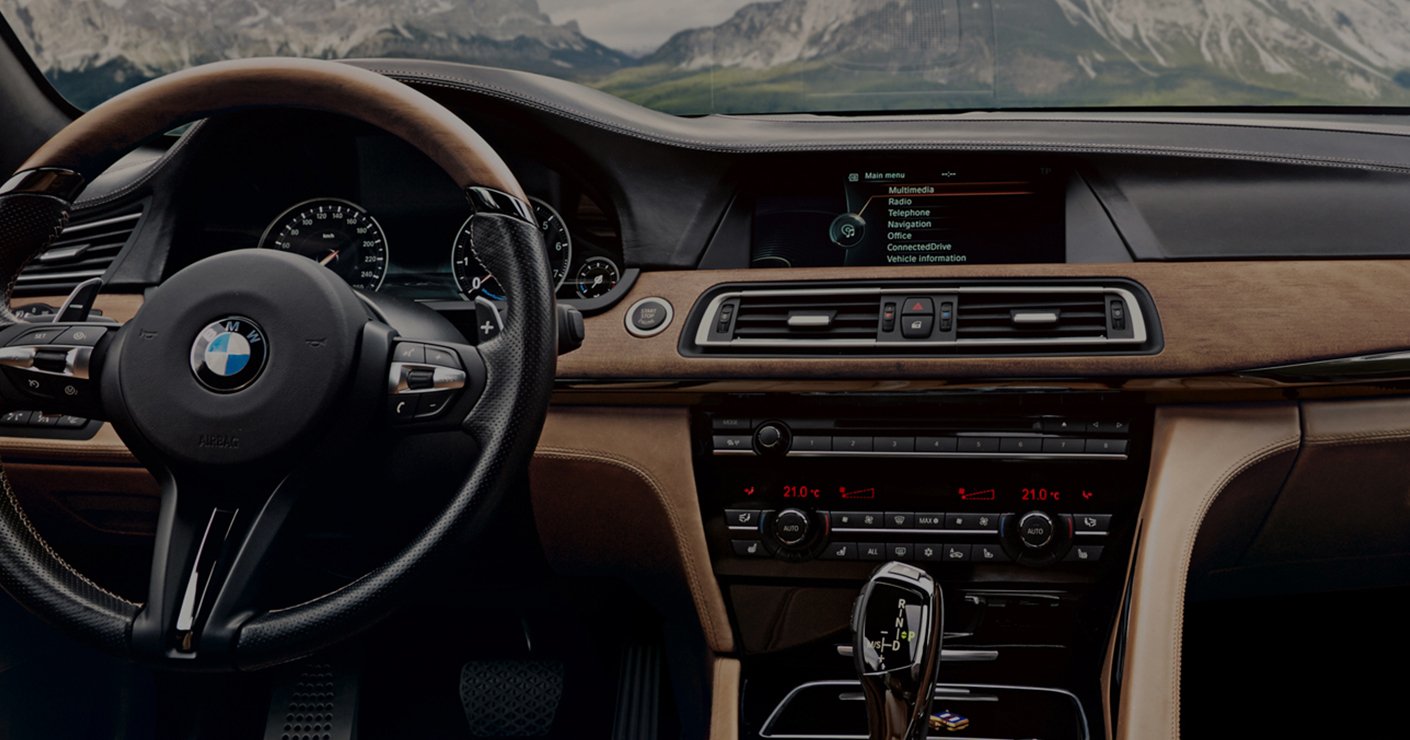